Introduction of Wire EDM Machining
Achieving the Impossible with Wire EDM Cutting Services
Ward Precision offers Micron Tolerance Wire EDM services, machining the “impossible” to achieve components most CNC machine shops are not capable of producing. Our very specialized Wire EDM services have high precision .001” wire capabilities allowing a corner radius of .0015”. We also offer micron positional accuracies – though 3µm to 5µm are more common, we have achieved positional accuracies of .05µm. We can achieve one-micron positional accuracy (0.5 micron was the best we’ve achieved under a special circumstance but 3 microns (.000118″) is more commonly achieved). We use a true 5 Axis indexing system , custom assembled by combining the efforts of a Japanese Control Systems company and a Swiss EDM company.
What is EDM
Electrical Discharge Machining – EDM – is the process of cutting/eroding material with an electric spark, created between an electrode and the metal component being machined. The electric spark, visibly showing the flow of electricity between the machine and work piece, produces temperatures reaching 8000 to 12000 degrees Celsius. This extreme heat can melt virtually anything. To ensure the surface of the work piece is the only part affected by the EDM, the spark produced is controlled and localized.
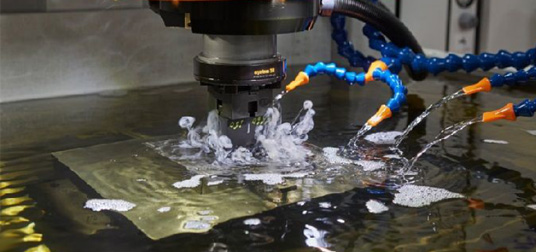
What is WIRE EDM
Ideal for machining delicate and complex parts, Wire EDM machines can be accurate to +/-1 micron and produce virtually no burrs (eliminating or greatly reducing the finish work required). Wire EDM machines are capable of machining work pieces up to 16” thick.
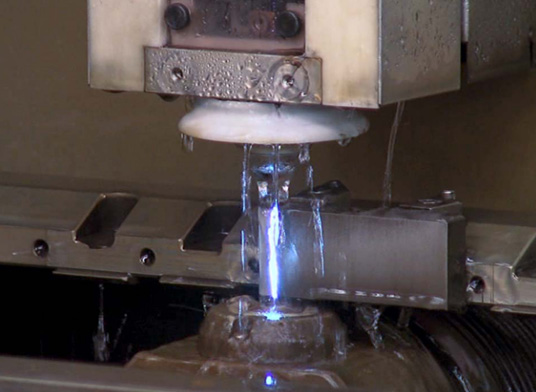
Wire EDM differs slightly from conventional EDM – the spark produced in Wire EDM always takes place in deionized water (the dielectric used for Wire EDM processes). Deionized water is used in Wire EDM because of its low viscosity, high cooling and material removal rate, and because deionized water is not a fire hazard. In Wire EDM cutting, a metallic wire (typically made of brass or stratified copper) between 0.1 and 0.3 mm in diameter is used to cut or rough/skim the part being machined. The wire used never comes into physical contact with the component being machined. The process used, and the specifics of that process, depend on the accuracy and surface finished required. Ward Precision’s experienced EDM machinists have decades of experience properly setting up, programming, and finishing EDM work from start to completion.
Benefits of EDM Wire Cutting
Additionally, extremely thin material can be accurately machined, because there is no contact between the piece and the wire. This eliminates distortions found in stressed cuts.